Peter: I am the fourth generation Limmer to make our hiking boots. I consider myself the steward of the company, not the owner, and I am grateful to all those before me. My great grandfather was a boot maker in Germany and his son, my grandfather, Peter Limmer Sr., was a master boot maker. My grandfather moved to the US in the 1920s because of Germany’s dire economic state at the time. He had a shoe factory in Bavaria with 15 people working for him; but, after leaving, the German government took everything. When he arrived in Boston with his wife Maria and their three children – Peter Jr., my dad, Francis, my uncle, and their sister, Elsie, who died at an early age – he had nothing.
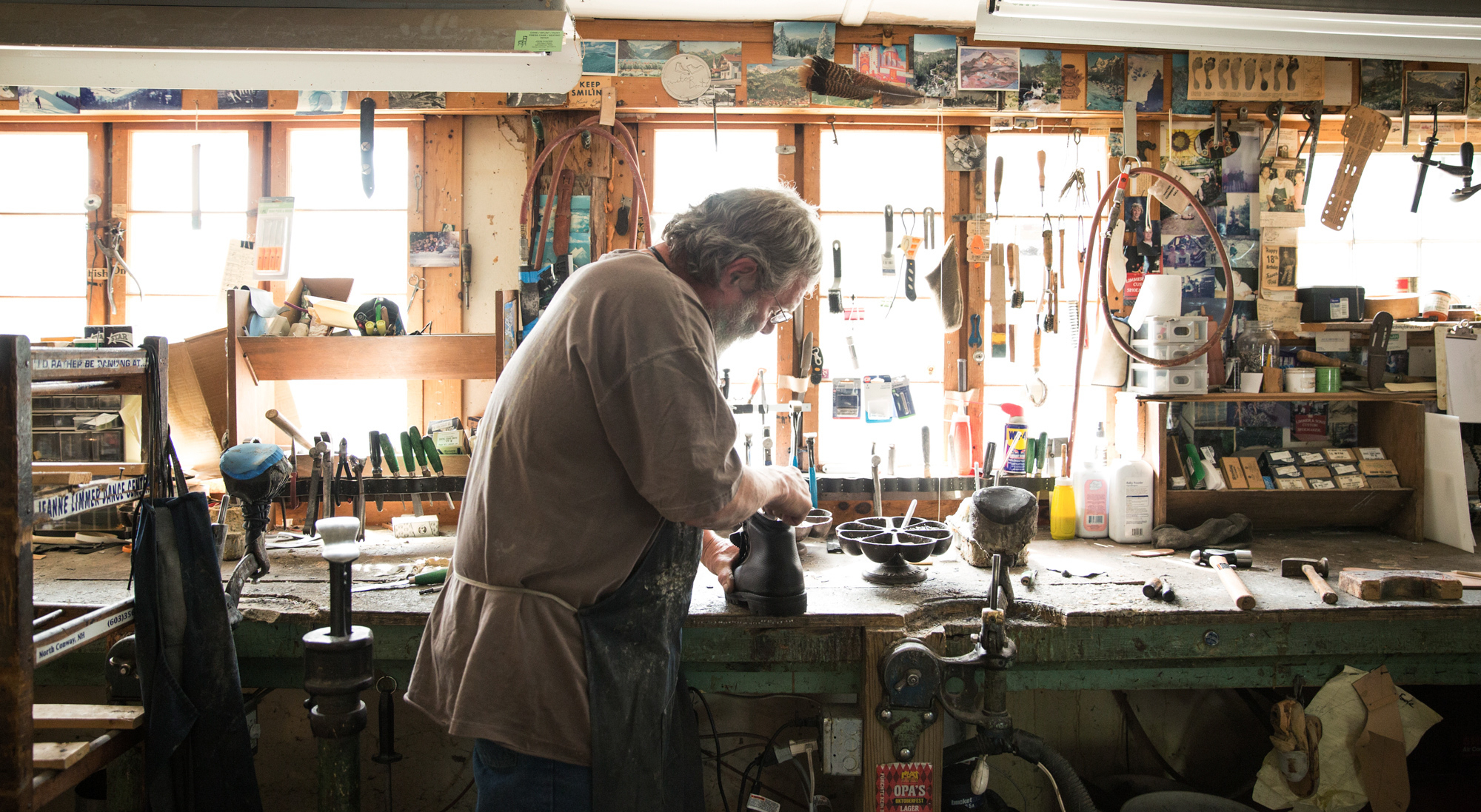
Made to Last
On the edge of the White Mountain National Forest in New Hampshire, USA, proudly stands the workshop of Peter Limmer & Sons. For the past 65 years hikers from all around the world have made their way to the quaint village of Intervale, NH, to reach the threshold of this unassuming building, for there awaits their coveted prize: a pair of Limmer-made hiking boots.
A feast for the senses, the dulcet sound of old blues music resonates through the low ceilinged workshop, and the air is heavy with the lingering smell of cut leather and old machinery oil. Vintage machinery fills the workspace, tools litter the workbenches, and memorabilia is plastered across every wall. Here, eager hikers looking for quality and longevity will have their new boots made and fitted by the two-person team, Peter Limmer and his cobbler, Ken Smith.
Limmer-made boots are much-sought after by the many who desire their own unique, handcrafted boots, enough to join the two-year waiting list to get them. Peter Limmer – the third ‘Peter Limmer’ in a long line of Limmers – tells the story behind one of the world’s most renowned custom boot companies.
Interview with Peter Limmer, photography by Greta Rybus
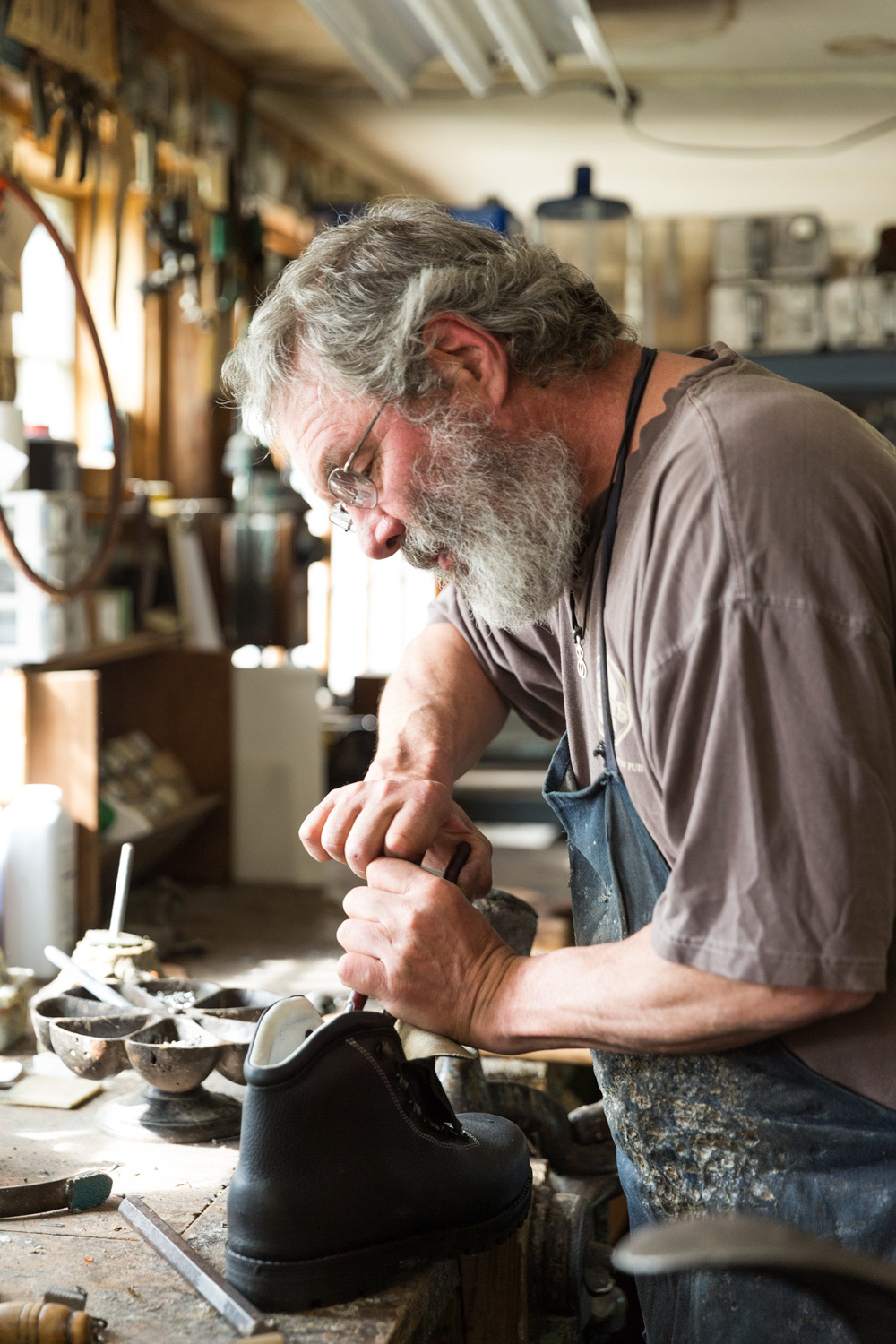
My grandfather moved to Boston to be near family already living there, and it was in Jamaica Plains – a Boston neighborhood – that he set up shop with his two sons, where they designed and made their own ski boots, hiking shoes, and hiking boots. After the military, my dad and uncle both would come to New Hampshire to ski. They mentioned to my grandfather that he should come up and see the area because it would remind him of his hometown in Germany. One visit and that was it; they packed up, hit the road and purchased the very same property that we are still working out of 65 years later.
As my cousin Karl, Francis’ son, and I grew up we began working in the shop as well, and, after my dad and uncle retired, it was us who took over the business. When making business decisions I always consider what my grandfather would do, but my cousin had different ideas. This led to us dividing the company: Karl went off and sold a copy of the Limmer boot as a private-label product to a company in Germany, and I continued with the custom boot building. I always felt more comfortable staying small and giving the customer the utmost care when it came to the boot build.
Today there are two of us here: my employee, Ken, who came to work for me 15 years ago, and myself. There have been some trials and tribulations with the economic state of the shoe industry, but after 40 years it has been a great run. I continually state that half my pay cheque is the great people I have been able to build boots for.
Did you always want to continue the Limmer family's boot making legacy?
I started working at the shop right out of high school. Back then vocation was the big push rather than avocation. But, I guess deep down I did, although I was never told that this is what I should do.
Have things changed much since the Limmer family began boot making; are you still using similar production methods and materials?
I am very fond of the fact that a lot of old timers come in and still feel comfortable enough to grab a chair and sit down and chat. I am still using a lot of the same machines my grandfather brought up here from Boston. That in itself is a chore, trying to keep the old stuff running, but I have always loved a challenge.
We have a government patent that was given to my grandfather back in 1939 for a ski boot that is hanging on the wall here. It gives us the bragging rights to say we made the first ski boot in the US. However, since the introduction of new technologies and materials in the ski boot industry, we no longer produce ski boots and instead now stick to creating beautiful, hard-wearing hiking boots.
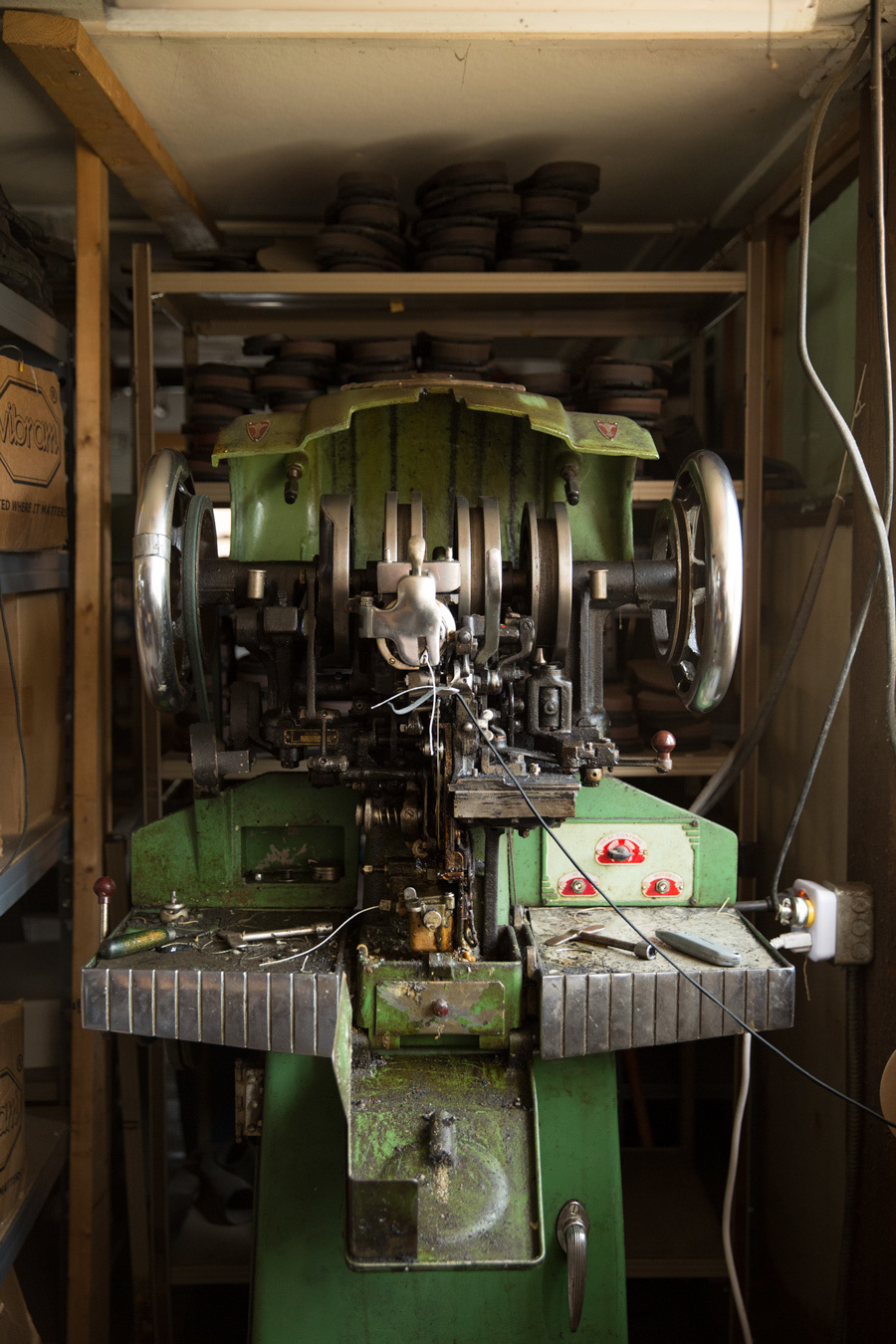
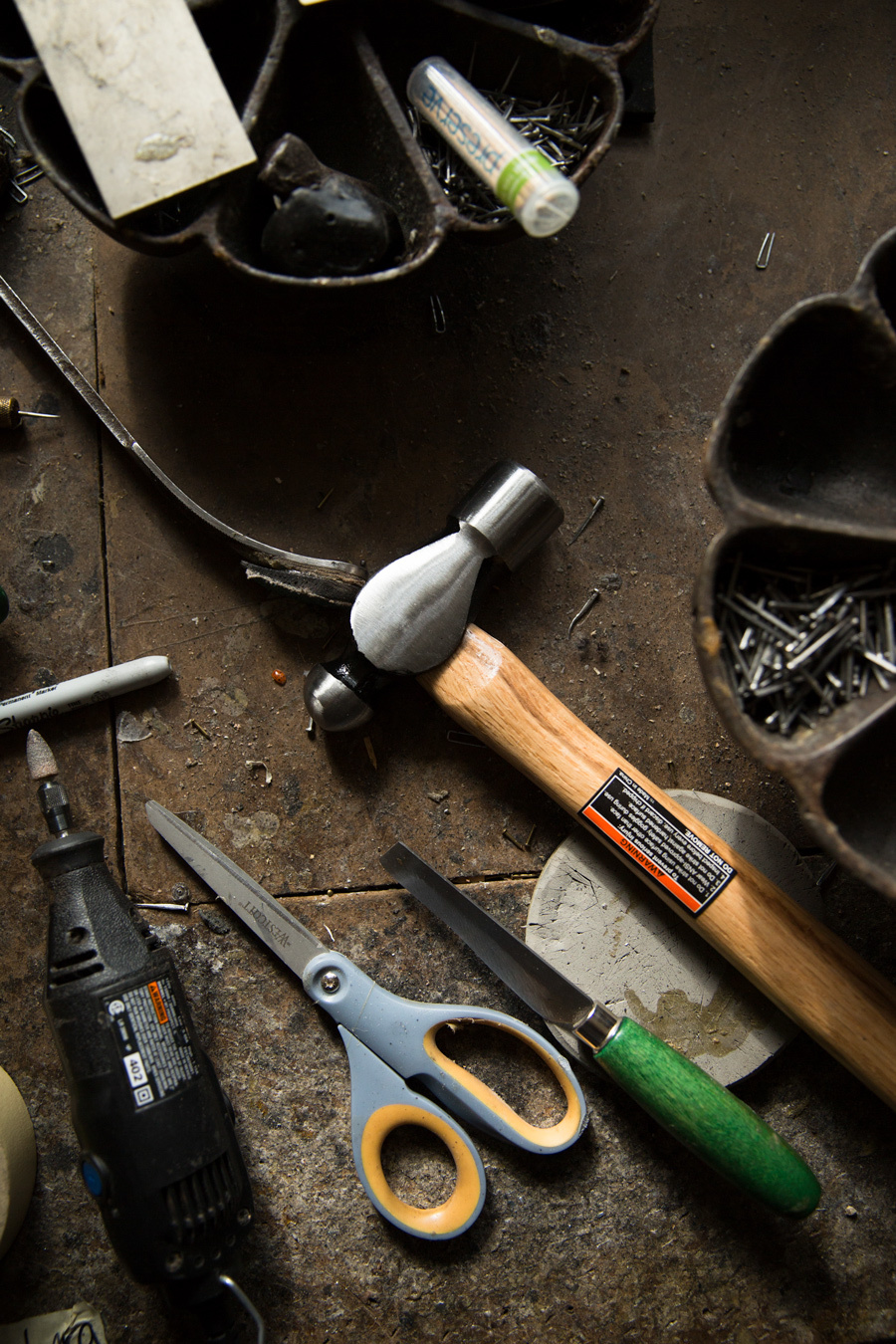
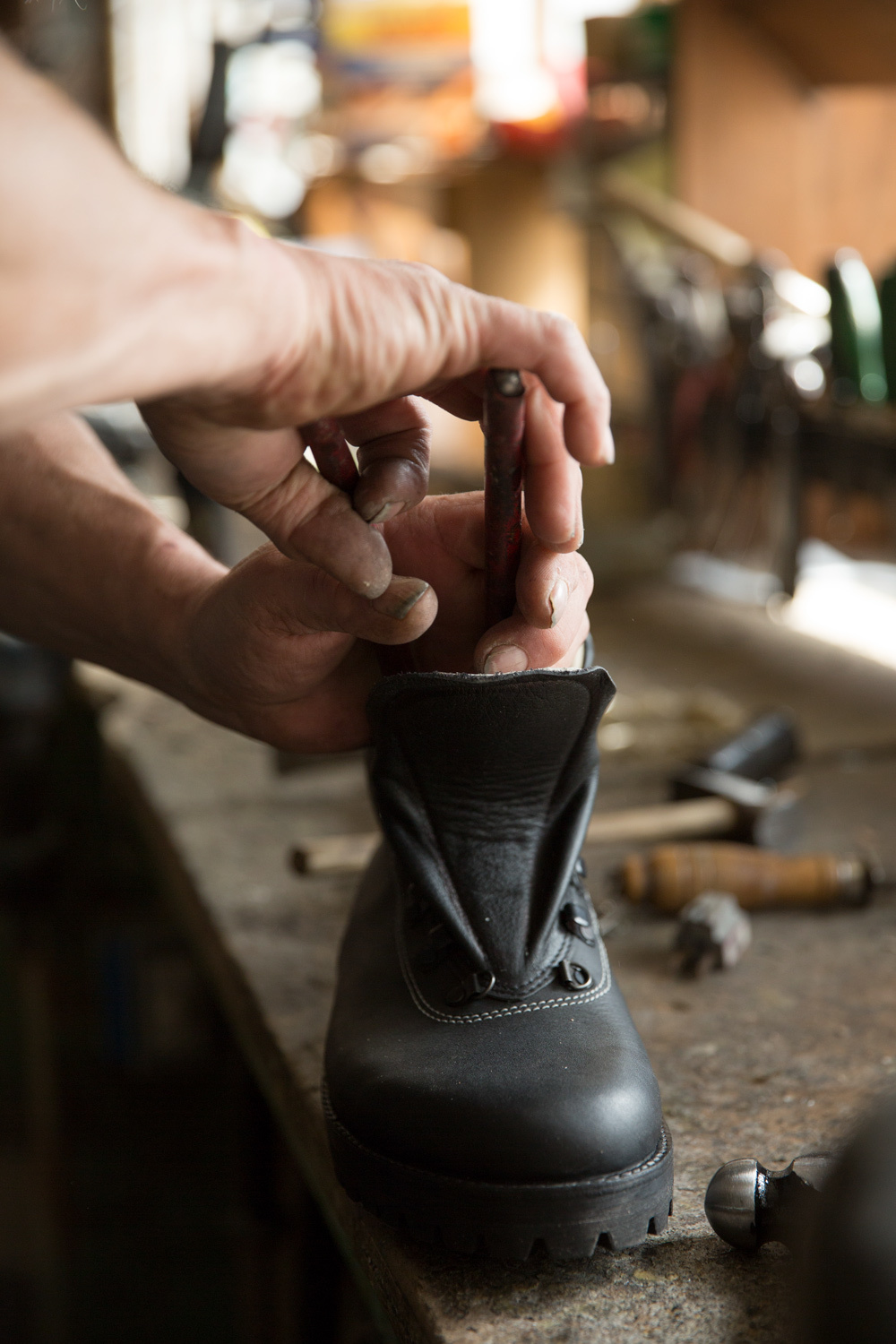
Could you please talk us through the production process of the boots?
First, I take all the measurements and a detailed tracing of the person’s foot. I transfer that to a wooden form called a ‘last’, which the boot is built from. Obviously, that requires the most amount of attention because if not right, the boot won’t fit properly. After the last is complete, it is a matter of stretching the leather over its wooden form. Then I read the leather for the pattern cutting, followed by a series of stitching, gluing, binding. However, there is a lot more to the whole process.
The boot is built with some of the best leather you can buy, and until recently I was buying my leather from Europe. The weak dollar finally made me start looking for a leather tanner here in the States, and I believe I have found a company that I hope will take me up to retirement.
How long does it take to make a pair of Limmer boots? It has been said that your customers may often have to wait for up to two years for a pair of Limmer boots.
There is a difference between the backlog, which is 18 months, and the boot build. I am fortunate to never have had to worry about where my next pay cheque was coming from because the lead-time has remained one year to 18 months the entire time I have been involved with the business. The boot build takes roughly 40 hours, although for every hour of hands on there is an hour of drying time. Because of this, I generally work on 12 pairs at a time, working through the pairs as the previous pair dries.
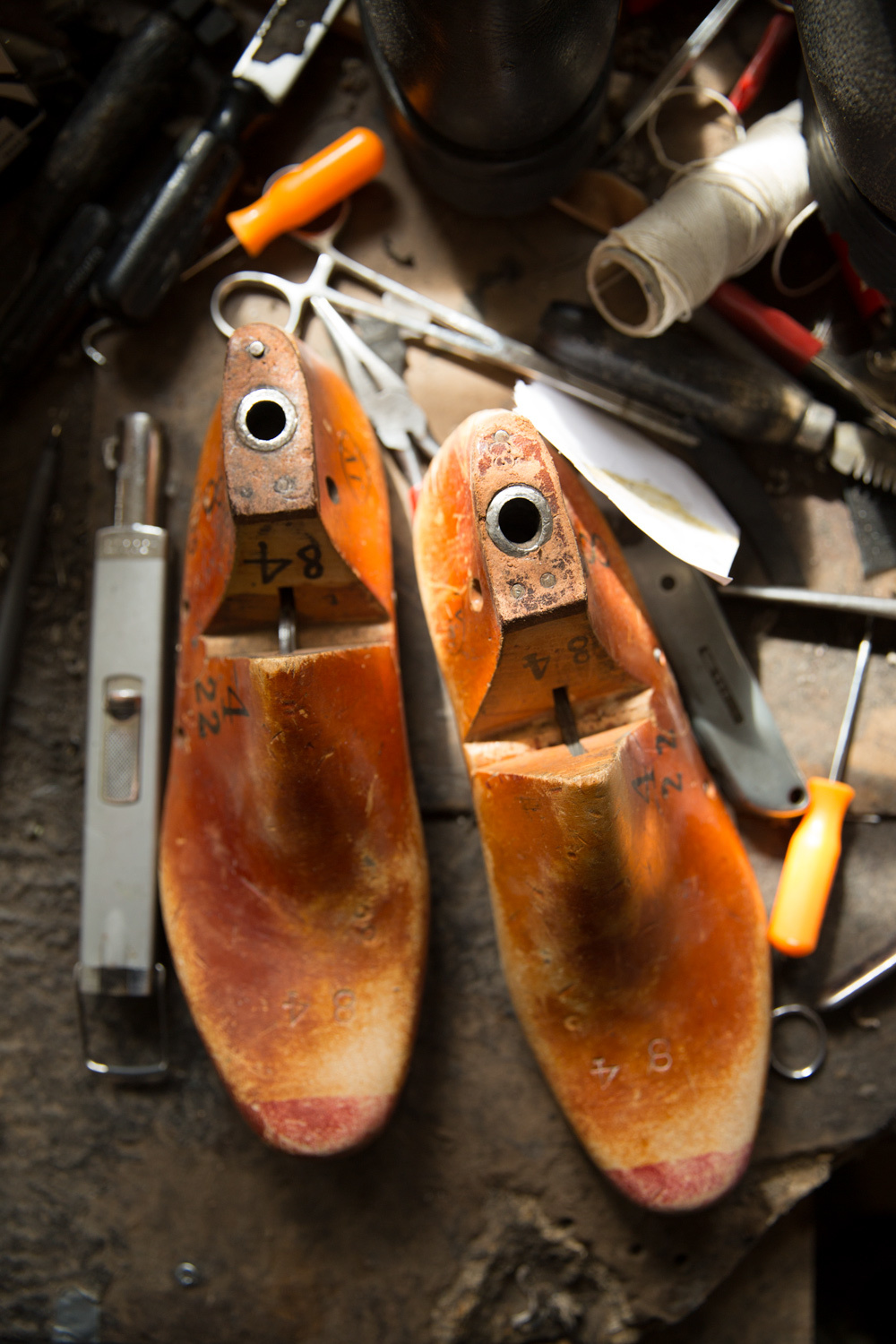
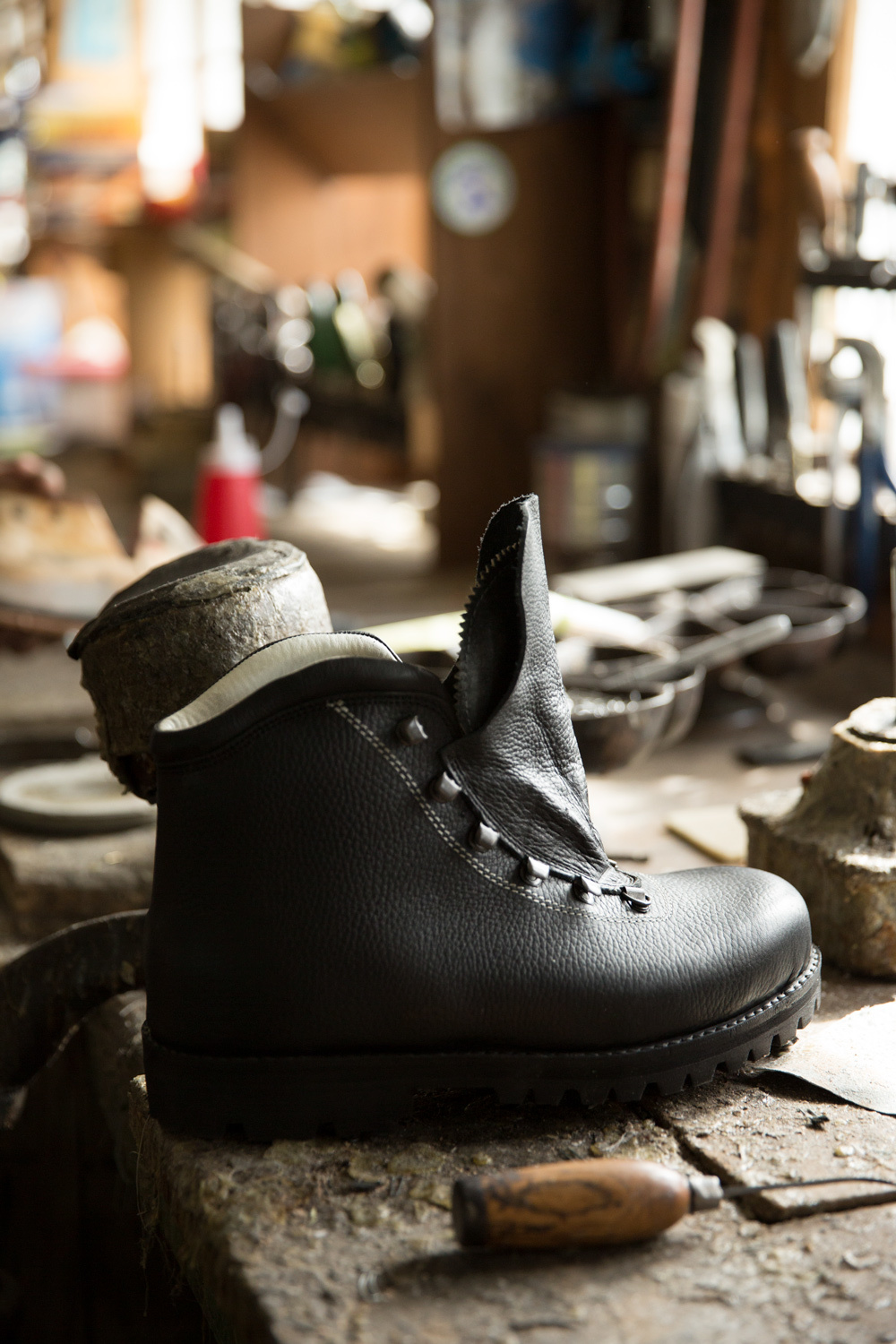
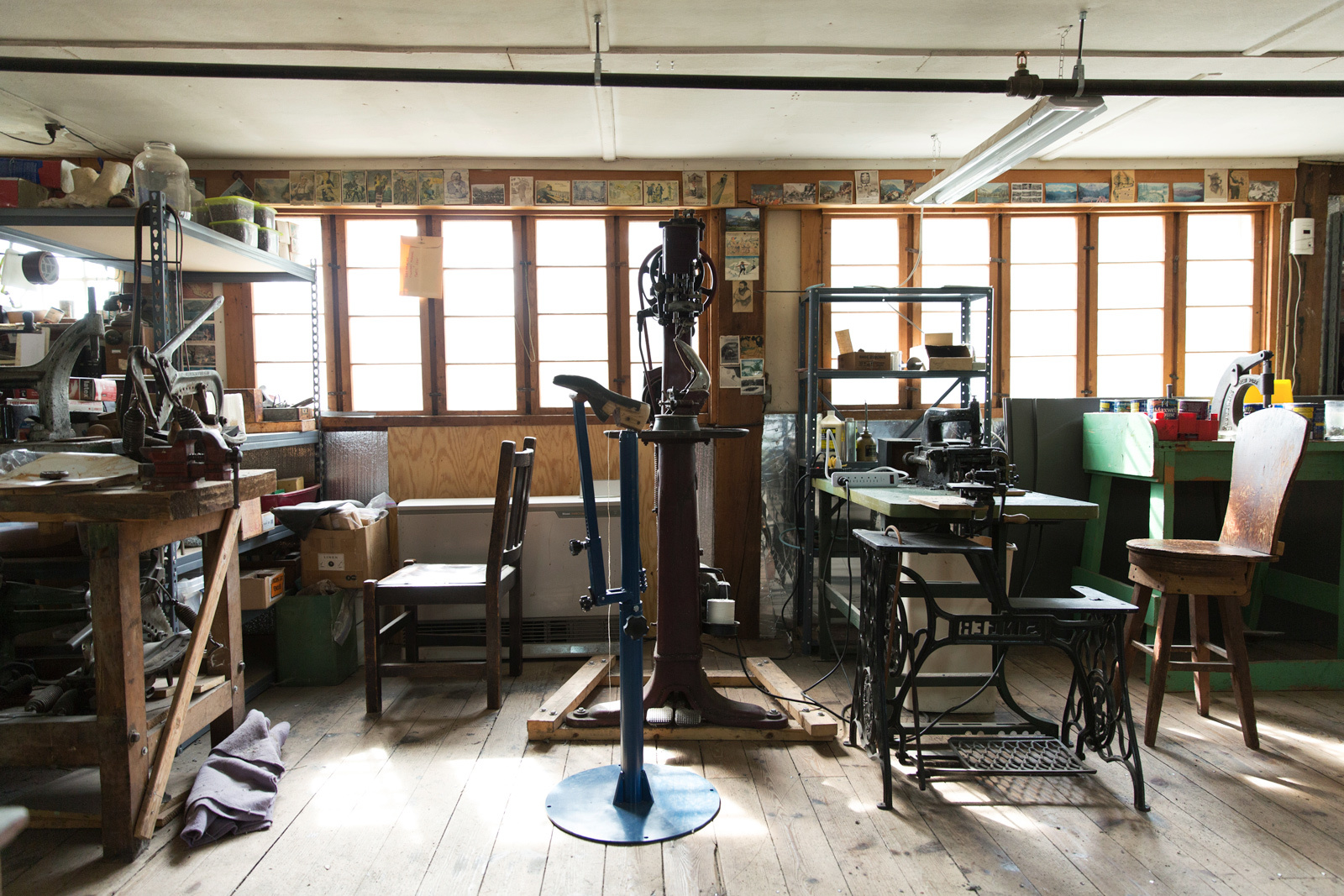
Have advancements in materials affected what you choose to work with or the way you craft the boots?
We are a niche product; we deal with the old-school hikers who know that ‘light’ and ‘long lasting’ just don’t go together. I do look at new materials and products, but in most cases there isn’t enough proof that it would be better than what I am using. If it’s not broken, don’t fix it!
It has been said that it is not unusual to have boots in your repair department that are over 50 years old. How does it feel to repair Limmer boots made by your father or grandfather?
That is always the cool part. I wish I had a nickel for every time someone said to me, “do you know how much money these boots have saved me over the last 20-30 years?” I hope to be producing the same quality of product, but only time will tell.
How do people find out about Limmer boots?
We have never paid a penny for advertising; it’s all word of mouth. Past customers are always getting in touch to tell us that they went somewhere and that someone either recognised the boots or asked about them.
I have sent boots all over the US and abroad as well. Whenever a boot is shipped to Europe I remember my Dad saying, “that’s like sending beer back to Germany”.
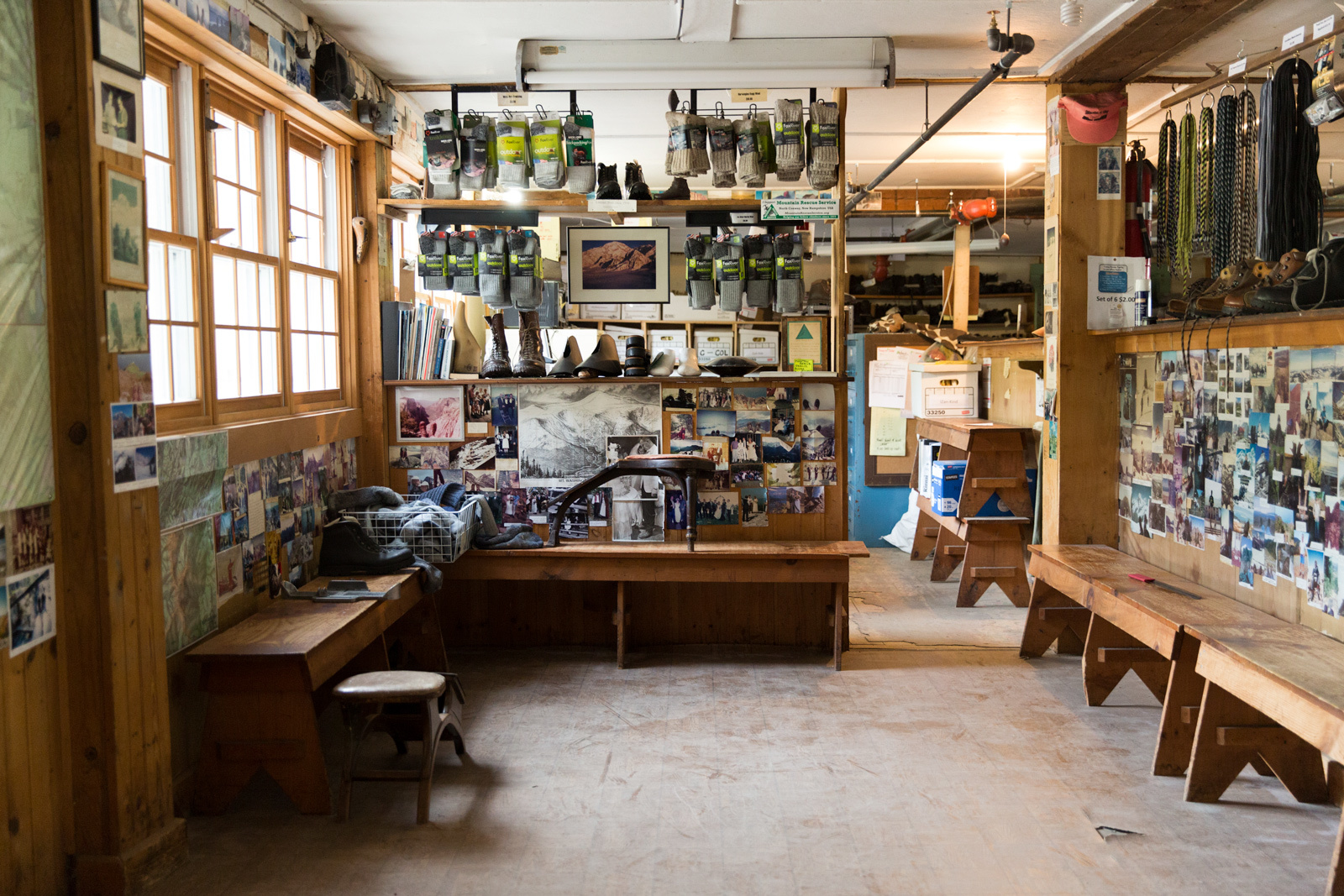

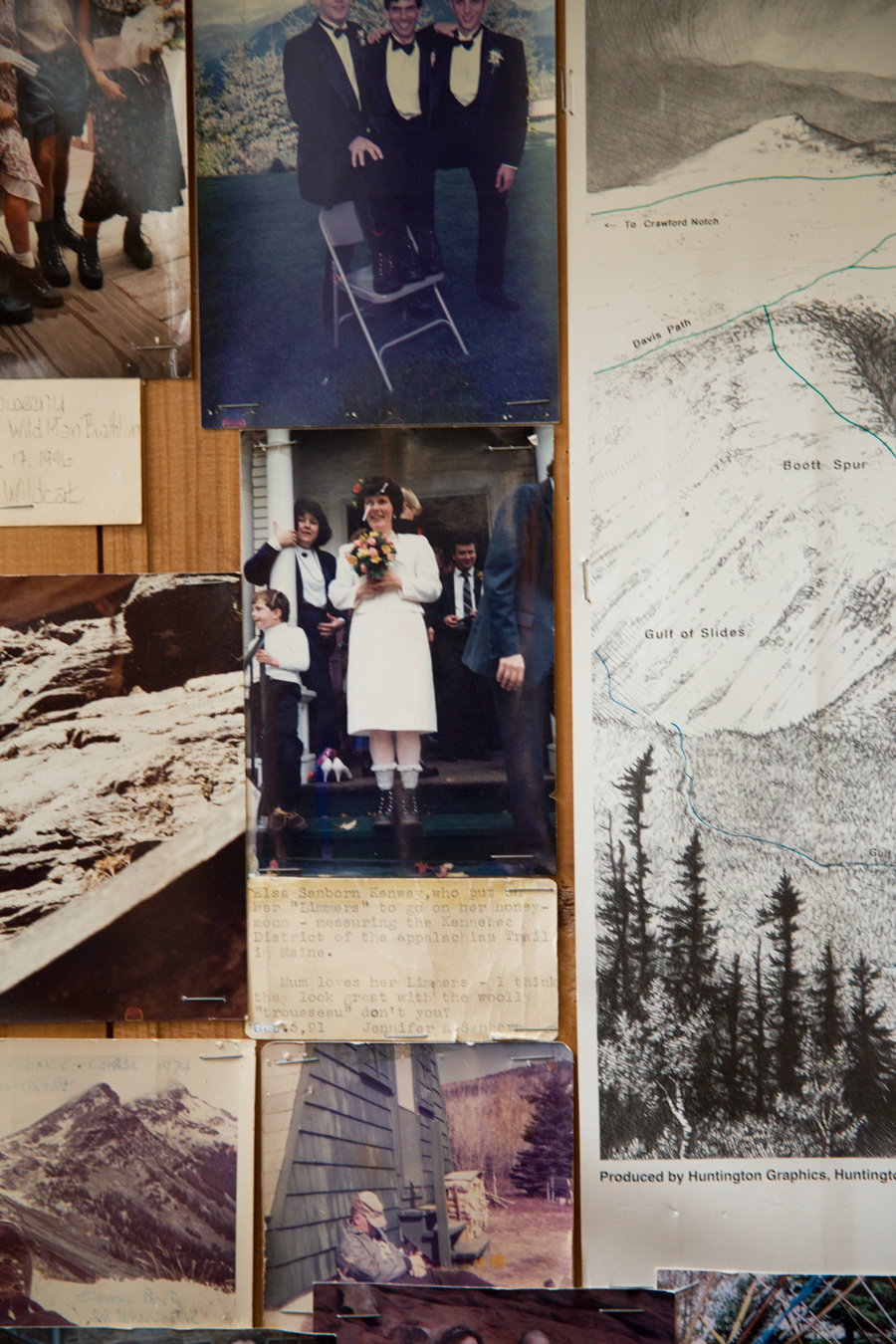
The Limmer customer wall of fame shows the positive sentiments your customers have for their Limmer boots.I have pictures from all over the world. Most of the highest peaks and all of the outstanding hikes around the world are on the wall. When people walk out of the shop with their new boots we always remind them that they have become part of our club and to send us a picture of themselves somewhere doing something, whether hiking or not. To this day I have a portfolio of pictures we can’t put up, most quite funny – it’s great to know that people think enough of us to send us them unabashed.
What is the most rewarding aspect of your work?
That it is an honest way to make a living. I do put in long hours and I don’t take as much time off as most people, but when you enjoy your work, it’s really easy to get caught up in it.
Also, working with my hands has taught and enabled me to tackle all sorts of other projects, whether it’s building our home, working on my vehicles or growing our own food; this is a satisfying and fulfilling by-product of making boots.
Are your sons likely to continue the family business?
Good question. I was never forced into the business and I feel compelled to be the same way with my boys. They enjoy the outdoors and work together in a landscaping business; they are very much sought after for their experience. Whatever they wind up doing, I will be proud of them as they always do the absolute best that they can. •
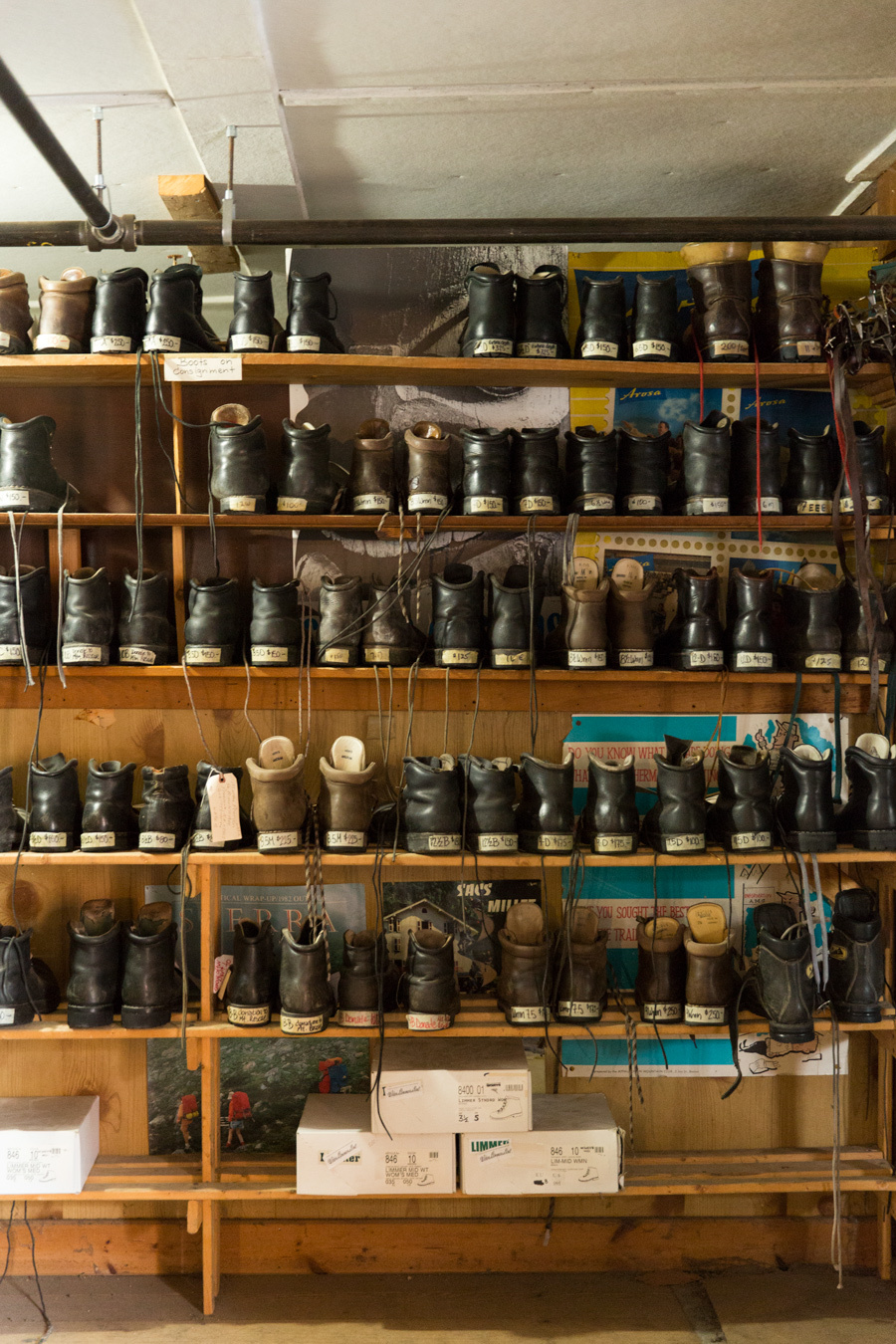
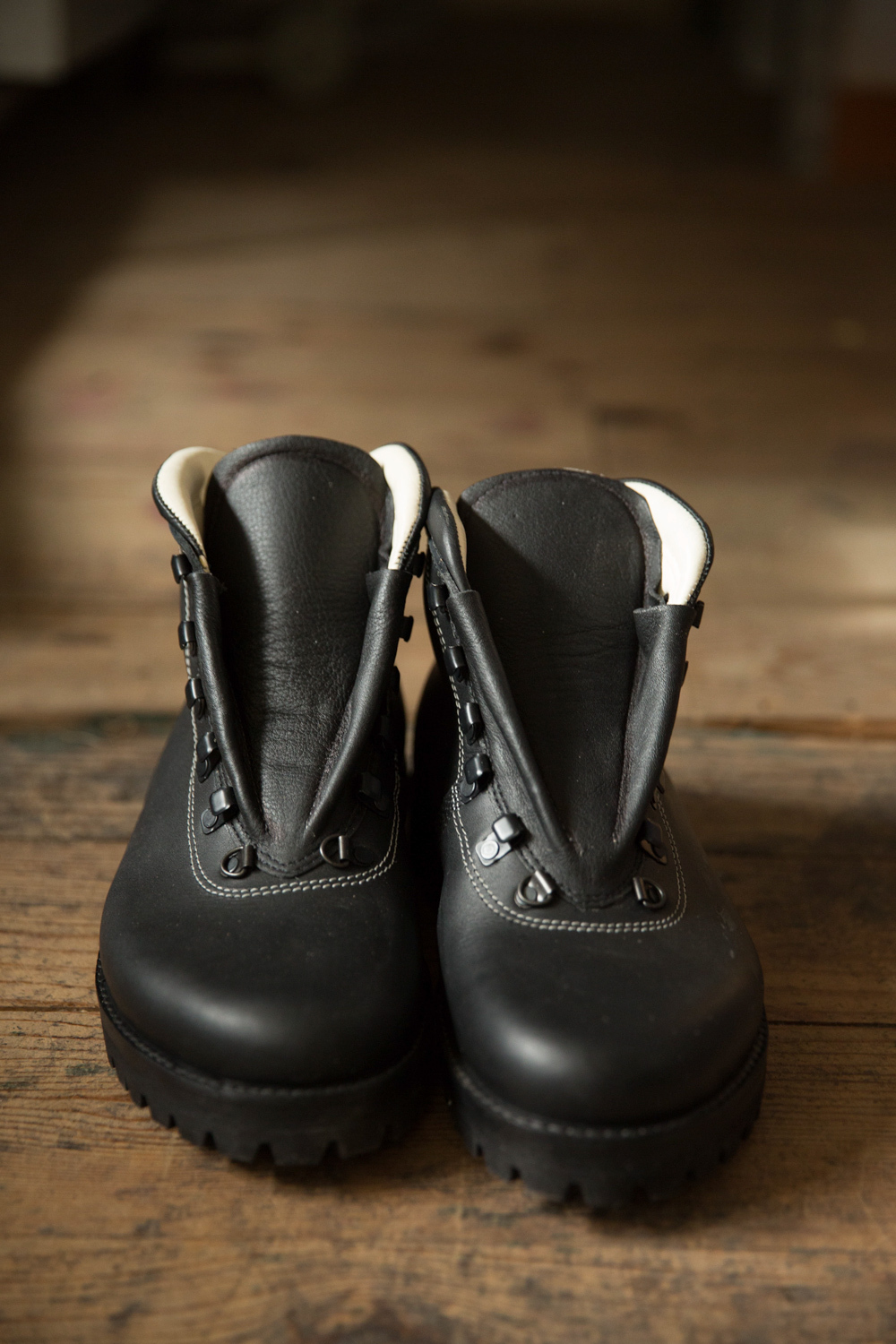
If you fancy a pair of Limmer-made boots then head over to Limmer & Sons website.
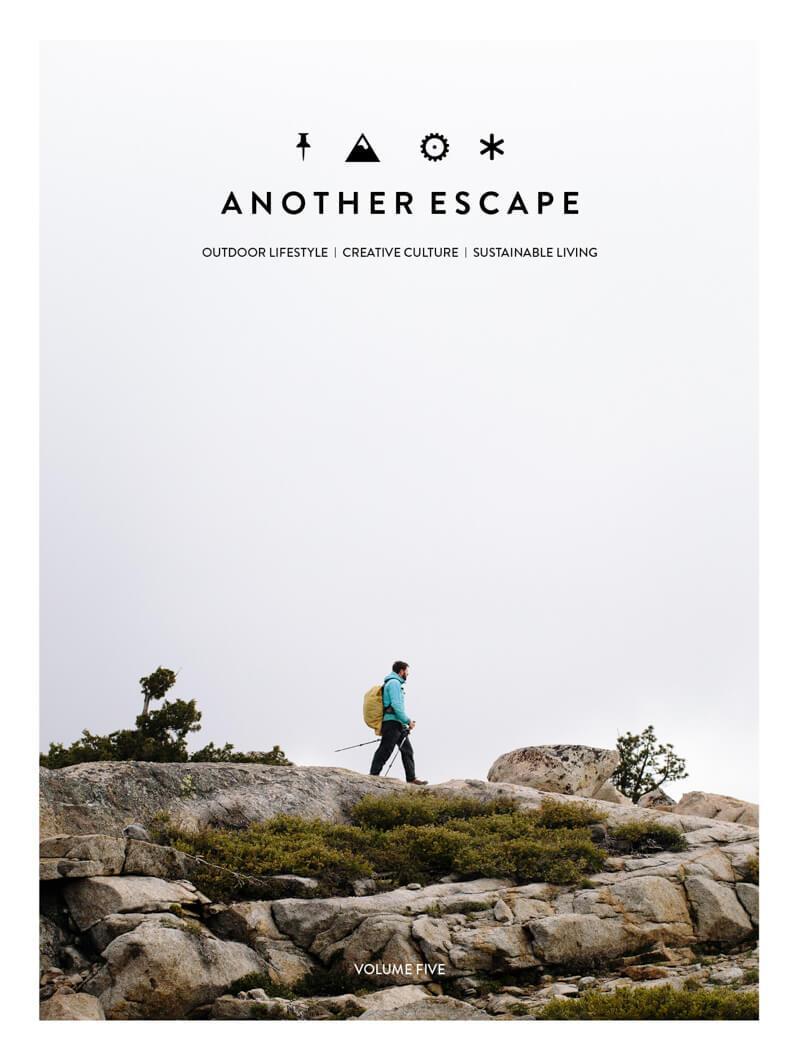